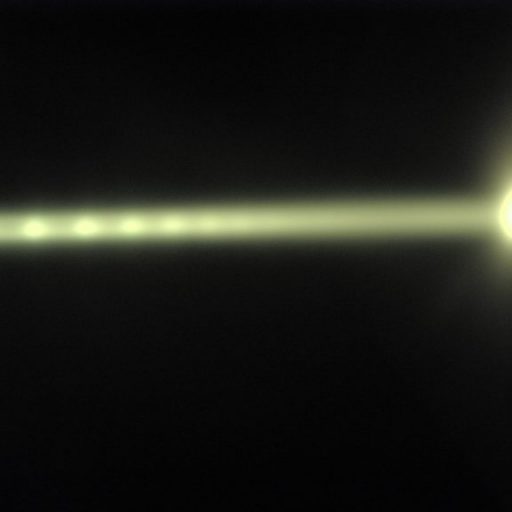
The HVOF (High-Velocity Oxygen Fuel) powder spray process is a thermal spraying technique used to apply high-performance coatings to various surfaces. In this process, a fuel gas (such as hydrogen or kerosene) and oxygen are mixed and ignited, creating a high-temperature, high-velocity flame. The heat generated by the combustion melts a powdered coating material (such as metals, ceramics, or composite materials), which is then accelerated by the high-velocity gas stream and sprayed onto the target surface.
This technique is widely used for creating wear-resistant, corrosion-resistant, and thermally stable coatings on components exposed to harsh environments, such as turbine blades, aerospace parts, and industrial machinery. The high velocity ensures a dense, strong bond between the coating and substrate, improving the durability and performance of the coated components. The HVOF powder spray process is particularly effective for applications that require enhanced material properties, offering significant advantages in terms of longevity, protection, and overall performance.
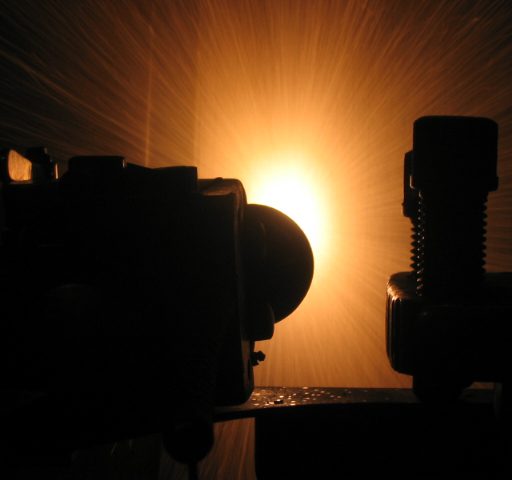
The HVOF wire spray process is a thermal spraying technique similar to the powder version but uses a wire feedstock instead of powdered material. In this process, a metal wire is fed into the combustion chamber, where it is melted by the high-temperature flame created by the combustion of a fuel gas (such as hydrogen or kerosene) mixed with oxygen. The molten metal is then accelerated by the high-velocity gases and sprayed onto the target surface, creating a dense, strong bond between the coating and the substrate.
The HVOF wire spray process is typically used for applications requiring wear-resistant, corrosion-resistant, and durable coatings. It is particularly beneficial for components exposed to severe mechanical stress and environmental conditions, such as in aerospace, automotive, and industrial machinery. This method provides superior adhesion, coating density, and durability compared to other coating techniques, making it ideal for parts that need long-lasting protection. The high velocity and the bonding created by this process improve the component’s resistance to wear and extend its operational life.